ෂෙල් අච්චු වාත්තු කිරීමයනු තාප සැකසුම් ෙරසින් සමඟ මිශ්ර වූ වැලි රත් වූ ලෝහ රටා තහඩුවක් සමඟ ස්පර්ශ වීමට ඉඩ සලසන ක්රියාවලියකි, එවිට පට්ටම වටා තුනී සහ ශක්තිමත් අච්චු කවචයක් සෑදේ. ඉන්පසුව කවචය රටාවෙන් ඉවත් කර cope සහ drag එක එකට ඉවත් කර අවශ්ය උපස්ථ ද්රව්ය සහිත කුප්පියේ තබා උණු කළ ලෝහ අච්චුවට වත් කරනු ලැබේ.
සාමාන්යයෙන්, ෂෙල් අච්චු වැලි සකස් කිරීම සඳහා සම්පූර්ණයෙන්ම මැටිවලින් තොර වියළි සහ සිහින් වැලි (GFN 90 සිට 140 දක්වා) භාවිතා වේ. තෝරා ගත යුතු ධාන්ය ප්රමාණය වාත්තු කිරීම මත අපේක්ෂිත මතුපිට නිමාව මත රඳා පවතී. ඉතා සියුම් ධාන්ය ප්රමාණයකට දුම්මල විශාල ප්රමාණයක් අවශ්ය වන අතර එමඟින් අච්චුව මිල අධික වේ.
කවච අච්චු ගැසීමේදී භාවිතා කරන කෘතිම දුම්මල අත්යවශ්යයෙන්ම තාප සැකසුම් දුම්මල වන අතර ඒවා තාපය මගින් ආපසු හැරවිය නොහැකි ලෙස දැඩි වේ. බහුලව භාවිතා වන දුම්මල වන්නේ phenol formaldehyde දුම්මල වේ. වැලි සමඟ ඒකාබද්ධව, ඔවුන් තාපයට ඉතා ඉහළ ශක්තියක් සහ ප්රතිරෝධයක් ඇත. ෂෙල් මෝල්ඩින් කිරීමේදී භාවිතා කරන ෆීනොලික් දුම්මල සාමාන්යයෙන් අදියර දෙකකින් යුක්ත වේ, එනම් දුම්මලයේ අතිරික්ත ෆීනෝල් ඇති අතර තාප ප්ලාස්ටික් ද්රව්යයක් ලෙස ක්රියා කරයි. වැලි ආලේප කිරීමේදී දුම්මල හෙක්සා මෙතිලීන් ටෙට්රමින් (හෙක්සා) වැනි උත්ප්රේරකයක් සමඟ 14 සිට 16% දක්වා අනුපාතයකින් තාප සැකසුම් ලක්ෂණ වර්ධනය වේ. මේවා සඳහා සුව කිරීමේ උෂ්ණත්වය සෙල්සියස් අංශක 150 ක් පමණ වන අතර අවශ්ය කාලය තත්පර 50 සිට 60 දක්වා වේ.
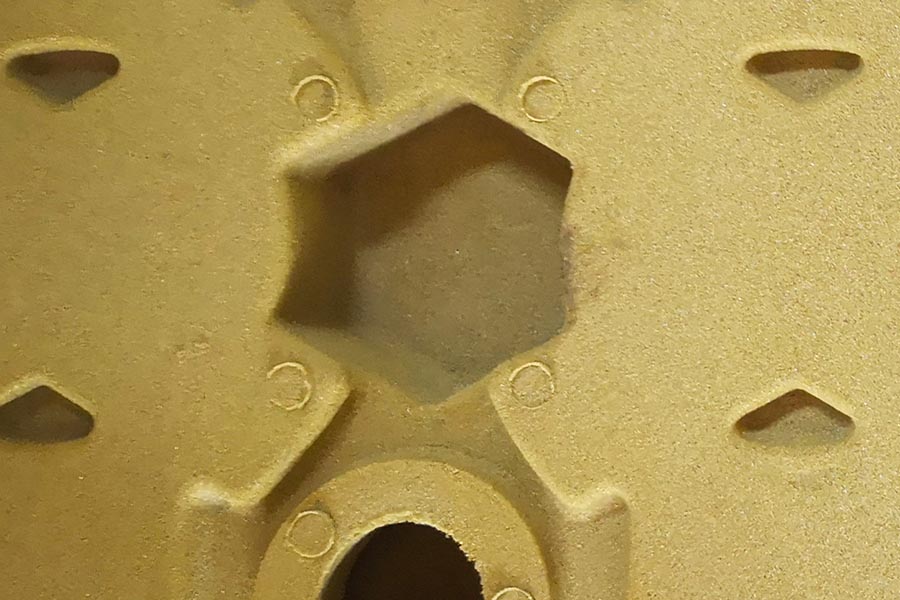
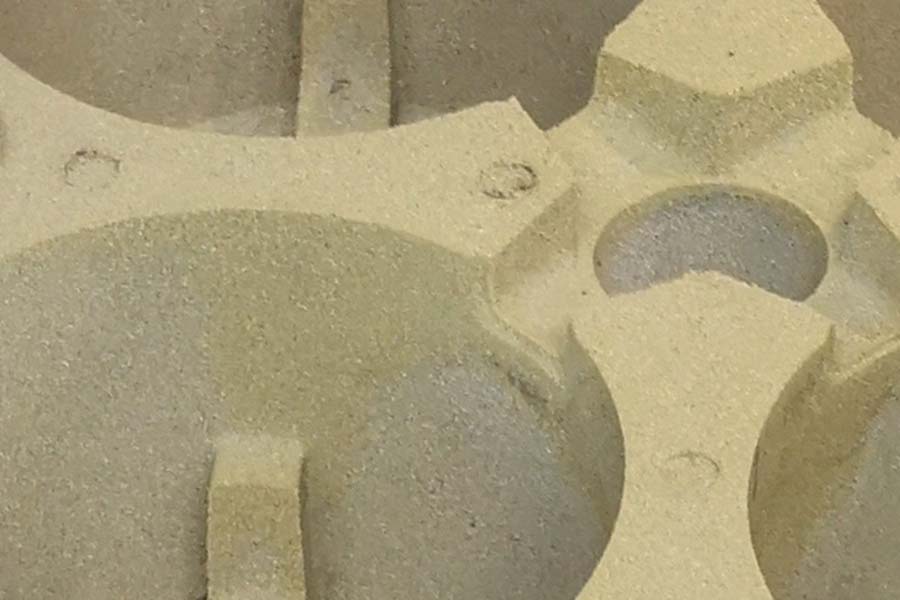
ෂෙල් අච්චු වාත්තු කිරීමේ ක්රියාවලියේ වාසි
1.ෂෙල්-පුස් වාත්තුවැලි වාත්තු වලට වඩා සාමාන්යයෙන් මාන වශයෙන් නිවැරදි වේ. වානේ වාත්තු සහ +0 සඳහා +0.25 mm ඉවසීමක් ලබා ගත හැකිය. අළු වාත්තු යකඩ වාත්තු සඳහා 35 මි.මීductile යකඩ වාත්තුසාමාන්ය සේවා කොන්දේසි යටතේ. සමීපව ඉවසා සිටින කවච අච්චු වලදී, විශේෂිත යෙදුම් සඳහා +0.03 සිට +0.13 mm පරාසයකින් එය ලබාගත හැකිය.
2. ෂෙල් වාත්තු වලදී වඩාත් සුමට මතුපිටක් ලබා ගත හැකිය. මෙය මූලික වශයෙන් සාක්ෂාත් කරගනු ලබන්නේ භාවිතා කරන සියුම් ප්රමාණයේ ධාන්ය මගිනි. සාමාන්ය රළුබව පරාසය මයික්රෝන 3 සිට 6 දක්වා අනුපිළිවෙලකි.
3. ට වඩා අඩු කෙටුම්පත් කෝණ වැලි වාත්තු, ෂෙල් අච්චු වල අවශ්ය වේ. කෙටුම්පත් කෝණවල අඩු කිරීම 50 සිට 75% දක්වා විය හැකි අතර, එය ද්රව්යමය පිරිවැය සහ පසුකාලීන යන්ත්රෝපකරණ පිරිවැය සැලකිය යුතු ලෙස ඉතිරි කරයි.
4. සමහර විට, ෂෙල් අච්චු ගැසීමේදී විශේෂ හරයන් ඉවත් කළ හැකිය. වැලිවල ශක්තිය වැඩි බැවින් ෂෙල් කෝර් අවශ්යතාවයෙන් සෘජුවම අභ්යන්තර කුහර සෑදිය හැකි ආකාරයට අච්චුව නිර්මාණය කළ හැකිය.
5. තවද, වාත-සිසිලන සිලින්ඩර හෙඩ් වර්ගයේ ඉතා තුනී කොටස් (මි.මී. 0.25 දක්වා) ෂෙල් මෝල්ඩින් මගින් පහසුවෙන්ම සාදාගත හැක, මන්ද අච්චු ගැසීම සඳහා භාවිතා කරන වැලිවල වැඩි ශක්තියයි.
6. කවචයේ පාරගම්යතාව ඉහළ මට්ටමක පවතින අතර එම නිසා වායු ඇතුළත් කිරීම් සිදු නොවේ.
7. වැලි ඉතා කුඩා ප්රමාණයක් භාවිතා කිරීමට අවශ්ය වේ.
8. ෂෙල් මෝල්ඩින් සම්බන්ධ සරල සැකසුම් නිසා යාන්ත්රිකකරණය පහසුවෙන් කළ හැකිය.
ෂෙල් අච්චු වාත්තු කිරීමේ ක්රියාවලියේ සීමාවන්
1. පැටන් ඉතා මිල අධික වන අතර එබැවින් මහා පරිමාණ නිෂ්පාදනයේ භාවිතා කළහොත් පමණක් ආර්ථිකමය වේ. සාමාන්ය යෙදුමක, ඉහළ රටා පිරිවැය නිසා අවශ්ය ප්රතිදානය කෑලි 15000 ට වඩා වැඩි නම්, වැලි අච්චුවකට වඩා ෂෙල් මෝල්ඩින් ලාභදායී වේ.
2. ෂෙල් මෝල්ඩින් මගින් ලබාගත් වාත්තු ප්රමාණය සීමා වේ. සාමාන්යයෙන්, කිලෝග්රෑම් 200 ක් දක්වා බරින් යුත් වාත්තු සෑදිය හැකි අතර, කුඩා ප්රමාණයකින්, කිලෝග්රෑම් 450 දක්වා බර වාත්තු කරනු ලැබේ.
3. ඉතා සංකීර්ණ හැඩතල ලබා ගත නොහැක.
4. රත් වූ ලෝහ රටා සඳහා අවශ්ය ඒවා වැනි ෂෙල් මෝල්ඩින් හැසිරවීම සඳහා වඩාත් සංකීර්ණ උපකරණ අවශ්ය වේ.
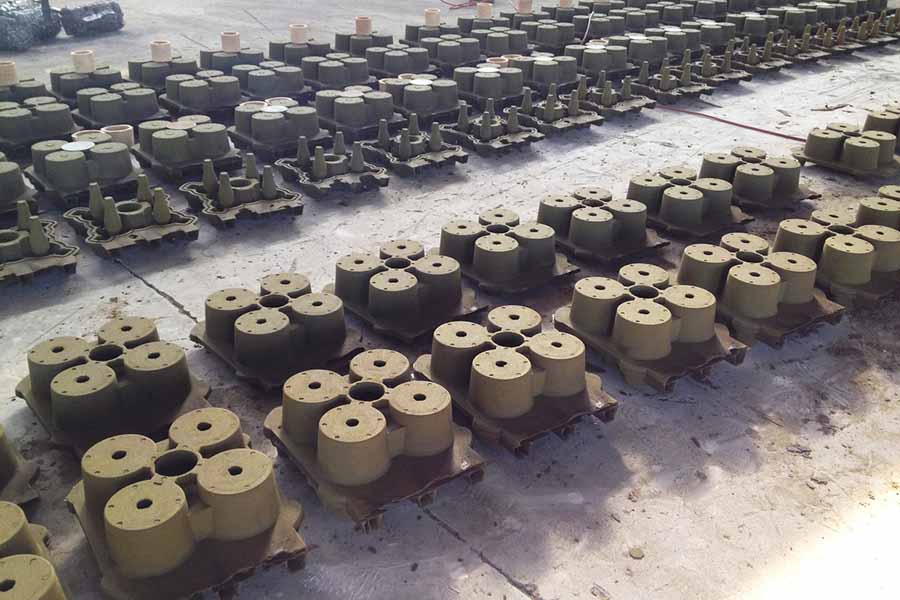
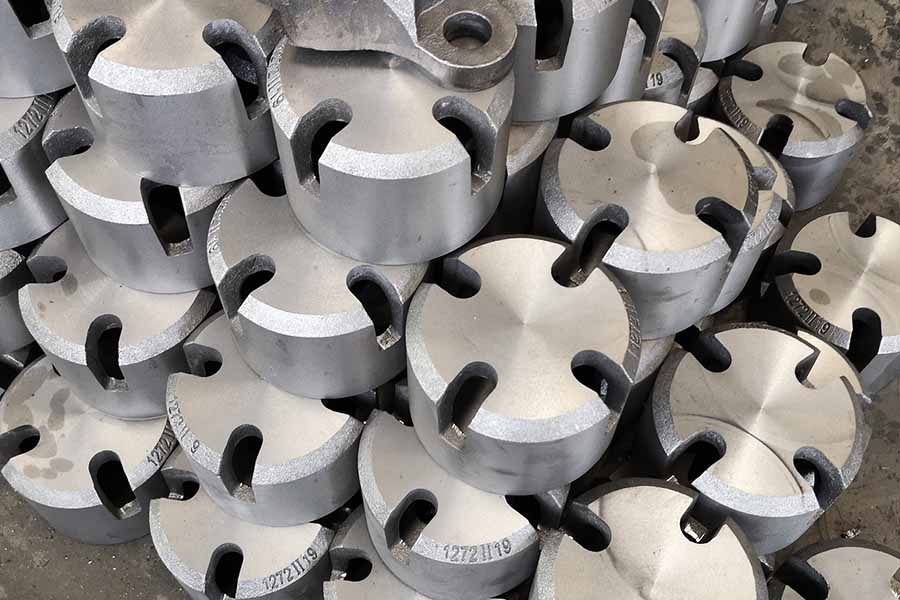
පසු කාලය: දෙසැම්බර්-25-2020